|
|
电话联系: |
021-60706467 |
|
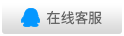 |
|
|
|
|
|
|
自动轨道运行小车输送系统中小车的监控 |
 |
2007-08-10 |
随着大规模集约化生产在国内的广泛采用,各类先进的自动控制输送系统不断出现,自动轨道运行小车输送系统(EMS)就是其中一种先进实用的系统并已在实际使用过程中体现出了非常明显的优点——故障率低,现场维护简单易行,能根据不同的需要实现不同的运行速度和动作,可以大大提高生产效率,实现柔性化生产的扩展。
运行小车的组成及功能
与其他输送系统相比较,自动轨道运行小车输送系统中的每台小车能根据要求在不同的位置实现以不同的输送速度运行、在不同的工作位置实现对所输送的物件安装高度和角度的调节,以满足生产对输送工件的节拍和位置要求。
在输送系统上的运行小车由传送电源和信号源的组件、控制器和电气元件以及驱动系统、载物输送架组成。
自动运行小车传送电源和信号源组件主要是由电刷及其支架组成,通过电刷和安装在导轨上的电排接触,使每台小车的控制器获得电源和速度信号以及实现小车控制器与中央控制柜的通信。小车的控制器是小车运行的大脑,用来向小车的驱动系统发送信号和实现每台小车和整个自动导轨系统中央控制柜的通信,同样在小车上的电器元件用来监控每台小车的运行状态,并传送回小车的控制器,然后由小车控制器反馈给中央控制柜。小车的驱动系统由马达、变速箱和驱动轮组成。小车上的载物输送架用于放置被输送的物件。
从组件来说,输送线由轨道、安装在轨道上的电排和沿线的感应开关或感应片组成。从功能来说,由输送段、工位段和诊断+维修段组成。
电排安装在小车运行的轨道上。电排一般有6根(见图1),其中三根为电源排L1、L2和L3,一根为接地排PE,一根用于中央控制柜向小车控制器传送信号的S1排,一根用于小车向中央控制柜反馈信号的S2排,小车通过安装在小车上的电刷和电排接触来获得电源和信号。
图1 安装在小车运行轨道上的6根电排 输送线的输送段纯粹用于物件搬运,输送速度较快,一般可达每分钟几十米甚至上百米。工位段的速度为慢速,一般最快为每分钟几米,并且是无级可调的。诊断+维修段是为了保证在输送系统中运行的小车能无故障运行,每当小车在系统中完成一个回路的运行后,对小车各个主要性能进行监控,如发现不正常状态可及时送入维修段进行维修后再投入系统运行。
运动控制
从图2中我们可以初步了解小车控制器与中央控制柜之间的关系。
图2 小车控制器与中央控制柜之间的关系 根据自行小车输送系统的特点,电排是沿着小车的运行导轨而布置的,系统的信号排S1用来加载不同的脉冲波,使小车控制器接收到脉冲信号后,能控制自行小车运行马达以不同的速度运行,而沿着小车的运行路线根据要求也布置一些感应开关,这是用来确定小车的位置,感应片用来感应安装在小车上的感应开关,使小车能进行翻转。图2中的开关1和开关2是安装在自行小车上的,当小车运行到一定的位置接触到感应片后将控制信号送到中央控制柜或小车控制器,以实现小车的其余功能。在图1中可以看到,在中央控制柜中有一台脉冲发生器产生不同的脉冲信号,假设脉冲波1与速度V1、脉冲波2与V2以及脉冲波3与V3分别对应,根据设计要求,小车需要在AB、BC和CD段分别以V1、V2和V3的运行速度运行,所以将信号排S1分割成AB、BC和CD段,通过电缆将脉冲发生器中的不同脉冲波分别通过电缆传送到电排S1上,根据预先确定的通信协议,当小车上的控制器根据所接受的脉冲信号来控制运行马达以相应的速度运行。如果假设小车是从A运行到B,中间以两种速度V1和V2运行,但是当小车从一种速度段运行到另一种速度段时是怎样实现平稳过渡的呢?
图3 小车运行速度变化的控制系统 从图3中我们可以看出,其实将AB、BC分割成AB1、B1B2和B2C段,在AB1段一直加载V1速度的脉冲波1,在B2C段一直加载V2速度的脉冲波2,而B1B2段被称为“速度交换段”,在该交换段加载的脉冲波信号随着小车在不同的位置而不同,那么怎样确定小车的位置呢?在小车的运行路线上安装有感应开关3、开关4和开关5,他们的位置关系将根据小车的长度来确定。如果后面的小车已在AB段开关3的位置,此时需要等待开关5检测前面的小车是否已离开速度交换段,如果检测到开关5为空,那么后面的小车将可以进入该交换段,如果位满,那么后面的小车需要在感应开关3的位置等待,直到开关5为空。而在B1B2段上的脉冲信号在小车进入感应开关4以前一直保持和AB1段的相同,即V1的脉冲信号,而当小车感应开关4检测到小车的时候,说明小车已完全进入速度交换段B1B2,并且感应开关4将信号传送到中央控制柜中的脉冲信号发生器上,脉冲信号器将V1速度的脉冲信号切换成V2速度的脉冲信号并加载到B1B2段上,这样当小车上的控制器接收到该脉冲信号后,小车的运行速度就从V1切换到了V2,V2的脉冲信号一直保持到小车被开关5检测到,说明小车已完全离开B1B2段,进入B2C段,这时开关5再向中央控制柜中的脉冲发生器反馈一个信号,将加载在B1B2段的脉冲恢复到V1的脉冲信号。
小车除了在系统中以不同的速度运行外,根据生产工艺要求,小车上的载物架有升降或翻转功能。现以小车的载物架在EF间翻转为例介绍其控制的实现(见图4)。在小车上安装有感应开关1和2,并且与小车上的控制器相连接,而在小车的运行线路EF上的E和F的位置分别安装有感应片,当小车运行到E时,触发感应开关1,并通过小车控制器启动翻转马达使载物架开始翻转,翻转的角度由安装在马达输出轴上的角度编码器监控,当达到预设的角度时,角度编码器同样将信号传送到小车控制器,使翻转马达停止运行,这时小车上的载物架将以一定的翻转角度输送物件到位置F。在位置F处的感应片将触发感应开关2,并将信号传送给小车控制器,并控制翻转马达将载物架向相反方向运转,翻转的角度同样由角度编码器监控,直到载物架回到原点,并将信号反馈给控制器,使翻转马达停止运行。其中监控载物架的编码器可以由两个限位开关代替,以达到监控载物架翻转角度的目的。
图4 载物架翻转的控制系统 对于小车上载物架的升降功能,其电气控制原理与翻转运动同理。
运行状态监控
由于输送系统中同时有多台或几十台小车同时运行,为了维修方便和及时,我们需要知道小车在输送线中的运行状态。
有时一条输送线长达几百米,小车在任何一个地方发生故障就会引起整个输送线不能正常运行,所以为了能及时发现小车发生故障的区域和具体故障原因,需要对小车在输送线的区域和故障原因进行定义。
从图1和图2中可知,每台小车上的控制器对小车的运行状态始终进行着监控,一旦小车在输送线中发生故障,将由小车上的控制器发出一个故障脉冲,并通过电刷传送到电排S2(通常该排上是没有信号的),而根据输送线的功能和长短,对S2排进行必要的分割,以定义不同的区域,并通过电缆再传送到中央控制柜的PLC中,这样就能在中央控制柜上显示出小车在哪个区域发生了故障,并停止向该区域的输送线提供动力电源。这样,维修人员就能很快确定故障区域,同时,小车上的控制器依靠内置的电源和预先设定在控制器上显示故障代码,以便维修人员方便地知道具体的故障原因,快速排除故障。
为了能有效降低信息传送量和PLC的信息处理量,由小车控制器检测到的各种故障被归纳到一个故障脉冲信号后被加载到信号排S2上,所以在中央控制室只能显示在某区域段有小车发生故障,而不能显示具体的故障原因,具体的故障原因需要到现场后,通过小车控制器才能知道。
为了最大限度地保证生产线的正常运行,当自行小车在输送线中每完成一个周期运行,空载的小车将进入自动诊断站对小车的刹车距离、启动速度时间是否正常,电刷是否过度磨损以及小车的接地等功能检测,如果检测结果为正常,则进入下一周期的运行,如果不正常,则自动进入维修段并显示不正常的功能。检修后的小车再次通过自动检测后才能进入输送线运行。诊断站实现了对小车的自动监测,大大降低了故障隐患,保证了输送线的正常运行。
自动轨道运行小车输送系统是国际上普遍采用的一种介体承载输送形式,在国内汽车行业的装配车间也已经被普遍采用,并且已经在实践中证明了其实际的使用价值。相信在整个制造行业,该输送系统都会找到自己的“用武之地”。
|
|
|
|
 |
|
|
 |
|
|